+491778419200
6Y Quality Services
Mass production and numerous suppliers can be a challenge when you require a stable and reliable quality.
We help manufacturers and their suppliers to minimize future quality risks, by going deep into the root cause and suggesting quality management changes.
​
Quality Management Implementation
When setting up a new manufacturing facility or a new line, best practice is to establish a Quality System to minimize the potential quality defects. We can help you to setup a robust quality management system from the start, or improve an existing one for future quality performance and smooth customer audits.
​
Standard we use is ISO9001, in addition to your own specific requirements.
​
Tools we use are:
-
APQP
-
FMEA
-
​
Supplier Audit
If you want to assess the capability of a potential supplier or develop an existing one we can support you with a whole-round technical audit of the factory.
​
This type of audit will include the basics of ISO9001 and a process deep dive as per your requirement, focusing on your engineering specifications.
Process Audit as per VDA 6.3
In case you are confident about the quality management and prefer instead a detailed deep dive into processes and make a risk assessment, we can perform a process audit for you.
For the process audit we use VDA 6.3 which is the original German Automotive Industry's standard for preventive process audits.
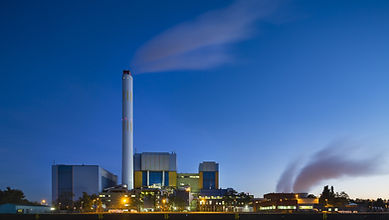
QUALITY MANAGEMENT setup
Summary
When setting up a new manufacturing facility or a new line, best practice is to establish a Quality System to minimize the potential quality defects. We can help you to setup a robust quality management system from the start, or improve an existing one for future quality performance and smooth customer audits.
​
Standard we use is ISO9001, in addition to your own specific requirements.
​
​​
Quality Management Setup Checklist
​
-
Quality Manuals and Standard Operating Procedure setup
-
Final inspection and Control Plan setup
-
Machine Maintenance Plan
-
Calibration Management setup
-
Inspection Tool Management setup
-
Internal System Audits setup
-
Internal Process Audit setup
-
Training Management including Technical Training setup and Qualification Matrix setup
-
Supplier Management and Incoming Inspection setup
-
Customer Satisfaction System setup
-
Claim Management setup
Project Scope and Reporting Process
​
First we hold a meeting with you to better understand your requirements, your product's technical specifications, quality targets and manufacturing processes. After that, we go through the departments at the plant on site to discuss the implementation. We write down our findings and suggested corrective actions in the report with the responsible staff that will implement the changes.
​
We will be in contact with the plant for the ongoing improvement process and arrange follow ups until the Quality Management Setup is at good level.
Supplier audit
Summary
If you want to an initial assessment of the quality management and technical capability of a potential supplier or develop an existing one we can support you on site. This will provide you an independent impression of the manufacturing of the supplier and enable you to minimize future quality risks.
​
This type of audit will be a comprehensive ISO9001 audit in addition to your specific technical requirements.
Supplier Audit Checklist
​​
-
Final inspection and Control Plan
-
Machine Maintenance Plan
-
Calibration Management
-
Inspection Tool Management
-
Internal System Audits setup
-
Internal Process Audit setup
-
Training Management
-
Sub-Supplier Management and Incoming inspection
-
Customer Satisfaction
-
Claim Management
-
Change Management
-
Environmental Compliance and Social Compliance basics as per ISO 14001 and OHSAS 18001.
And your own requirements...
Project Scope and Reporting​
​
First we hold a meeting with you to better understand your requirements, your product's technical specifications, quality specs and manufacturing processes. After that, we go through the departments at the plant on site and audit the departments. We present the findings to the supplier at the end of the audit and send you the findings and the suggested corrective actions.
​
According to the assessment we can do a follow up audit after the corrective actions are implemented by the supplier.

Process Audit as per VDA 6.3
Summary
In case you are confident about the quality management and prefer instead a detailed deep dive into your own or your supplier's processes to make a risk assessment, we can perform a detailed process audit for you. This type of audit is proactive in nature that will promote risk management in the production.
​
For the process audit we use VDA 6.3 which is the original German Automotive Industry's standard for preventive process audits.
​
Process Audit Checklist per Process
​
-
Control Plan
-
Input-Output analysis
-
In Process Inspections and AQL
-
Inspection Tool Management
- Machine Maintenance
- Staff Qualification and Training
- Rejection areas and Reg-Green tags
- Kanban and Traceability
- 5S
- Tool Calibration and Calibration Management
And your own requirements...
​
Project Scope and Reporting
​
For process audits we will first hold a short meeting with you understand the targeted product characteristics and the corresponding processes and hold the audit on site. Process audits normally take 2 to 4 days, and this can be decided as per how many processes is going to be audited and how comprehensive of a span is needed at the manufacturing
​
After the audit is finished we report you the findings with suggested corrective actions, and we can do a follow up audit if needed.

Part inspection
Summary
We can support you at both on site part inspections and part inspection methodology check.
​
It is important to be on the same page regarding calibration both at the supplier and the OEM side when inspecting products. Our usual process starts with quality management check of calibration management.
In addition to setting up an AQL system we can implement a statistical process control (SPC) for your crucial characteristics to enable the pre-detection of a quality failure that is around the corner.
Part Inspection Checklist
​
-
Control Plan
-
Final Inspection SOPs
-
Tool Calibration
-
AQL (Acceptable Quality Level) and Sample size
-
Calibration Management
-
Rejection Areas
-
SPC (Statistical Process Control)
-
Inspector Training
-
MSA (Measurement System Analysis)
-
Lab Management
​
And your own requirements...
Project Scope and Reporting
​
After we hold a meeting with you to understand your part specs and technical drawing we define the necessary inspection methods together, if there are any special lab equipment is needed as per your requirement.
​
Later on we go on site to inspect the part, according to the required sample size and by picking a random sample. When doing these producers's documentation, SOPs, Kanban card and other items in the checklist are taken into consideration. You receive the inspection report on the same day.
